5 Problems With Welds, Rivets and Bolts in Military Products
Posted on Fri, Aug 15, 2014
When you’re designing and building a military product, it’s important to consider the long-term endurance and product weight. You want to ensure optimal function, making sure your assembly methods give your product the longest life-span possible.
Using assembly processes that drill holes can potentially diminish your product's lifespan and can be more costly than newer fasteners on the market today.
Welds, rivets and bolt holes limit your options, especially when using lightweight materials. Attaching components using an adhesive fastener speeds assembly, distributes the bond line pressures, and can ultimately help extend the lifespan of the device.
Below are five reasons why you should avoid limited assembly methods and instead opt for a lighter-weight solution developed from 3M attachment products.
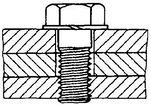
1. Holes speed deterioration. Any time you drill a hole in something, you open that item up to corrosion, rust and contamination, because of exposure to the elements inside and out.
2. If you drill it you, must seal it. Once you drill a hole in a material, you’ve got to add new components to protect that hole from deterioration. This drives up manufacturing costs by adding sealants or reinforcements. If you assemble your device using a no-drill attachment solution you save on both materials and labor costs.
3. Heavier overall weight. Rivets and welds require heavier base materials, making a product heavier. Adhesive and tape solutions can be used on lighter-weight materials. Combined, these solutions have numerous advantages from energy savings, to reduced waste and increased product portability.
4. More equipment and higher labor costs. With rivets and welds comes a need for the tools and specially-trained people to do the work. Alternative attachment solutions don’t require heavy-duty tools and have lower-labor costs, and consequently provide cost savings.
5. Mistakes are permanent. Once you drill a hole or make a weld, there’s no going back if you realize the geometry was off. 3M attachment solutions have varying degrees of green strength and adjustments can be made.
Starting a conversation with a Tape & Adhesives Converter
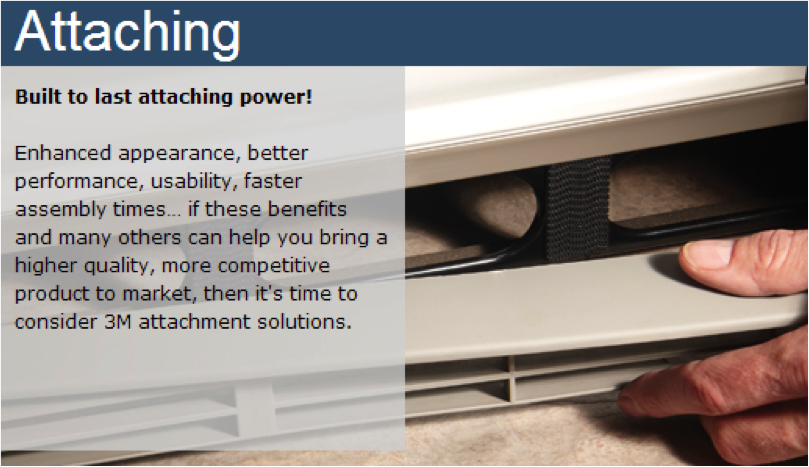
If you’re interested in exploring assembly alternatives to rivets and welds you can contact Gleicher Manufacturing Corp.
Gleicher's a 3M preferred converter who will help you explore product options.
Our experts can walk you through different product families that are available, then help select the specific 3M product that best suits your project needs.
When evaluating fastening options it’s important to consider not just environmental exposures, but also the production assembly process. Starting a conversation with the converter during R&D can help ensure that you get a production-ready sample to ensure accurate prototype testing. And this also means a smoother production process in the end.
Resources: