Medical Device Assembly - a collaboration helping prototype to market
Posted on Wed, Feb 19, 2014
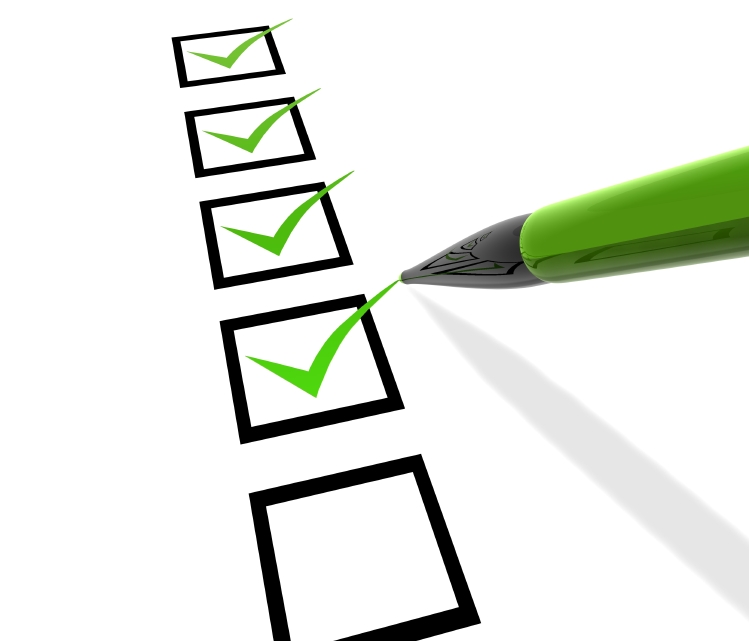
The big manufacturers always seem to get products to market on time and on budget.
But with so many unknown variables in the prototyping process, they must have a secret recipe, right? How do they get better prepared for each test?
It turns out the magic is in the details.
We took a look at some successful product launches to see how those Engineers achieved success in their programs.
Nothing is more frustrating than creating and destroying prototypes because of inadequate testing samples. You know the cause: you can't replicate the real-life production environment because of time, budget or access to materials. Often, temporary solutions are used for fasteners. That can be the failure that results in another destroyed prototype. A bad fastener lowers yields and raises costs.
Sneak a peek at the process used by the most successful teams; better prototypes require production-ready samples.
Here's the formula the quickest teams are following to get the best prototypes and the best production: Design, Source, Convert.
By establishing a detailed profile of exposures during the design stage, you substantially narrow the options for sourcing the right fastener materials. The best teams spend time analyzing the interactions of environment and stresses, combined with the chemistry of the materials being joined, before even proposing a tape or adhesive.
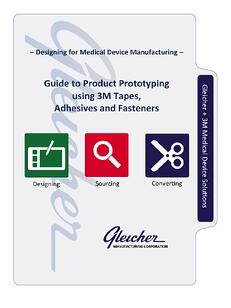
But they don't stop there. Making it all the way through production means designing for manufacturing. Factoring in the assembly infrastructure and processes are just as critical to understand if the device is to sail through production. The most successful programs collaborate early with their converting teams.
Learn the secrets to getting the highest possible yield at the lowest possible cost. Download the Guide to Product Prototyping using 3M Tapes, Adhesives and Fasteners.